Choosing the Best Gutters for High-End Architecture
Unlike standard homes, luxury properties demand gutter systems that offer both historical accuracy and modern durability. The following considerations should guide an architect’s selection process:
1. Architectural Compatibility
A gutter system should blend effortlessly into the home’s exterior, respecting the historical and stylistic integrity of the design. This is particularly important for:
Classical & Historic Homes – Many traditional estates and historically inspired residences originally used wood gutters, requiring an authentic replication without the drawbacks of wood maintenance.
Modern & Contemporary Homes – Minimalist designs benefit from gutters that either become invisible elements or serve as intentional design details, aligning with sleek facades.
Best Choice: Duragutter’s historically accurate profiles ensure seamless integration into both classic and contemporary luxury home styles.
2. Material Selection & Durability
Luxury homes require materials that align with architectural quality while ensuring longevity. Traditional options like copper or wood-lined gutters can be costly and high-maintenance, making extruded aluminum gutters a superior alternative.
Best Choice: 1/8” T5 extruded aluminum gutters offer unmatched durability, won’t sag or warp over time, and can be custom-painted to blend with the home’s exterior palette.
3. Customization & Aesthetic Versatility
For luxury home gutters, flexibility in color and profile selection is key. A system that can be customized to match trim details or remain visually discreet is highly valuable in architectural design.
Best Choice: Duragutter’s powder-coated finish provides a premium, long-lasting aesthetic that can be painted in any color to match custom exterior detailing.
4. Installation & Performance Efficiency
Even in high-end homes, functionality cannot be compromised for the sake of aesthetics. The best gutter systems offer:
Precision-engineered designs that simplify installation
Seamless joints that prevent leakage and structural damage
High-capacity drainage that protects against water overflow, crucial for residences with complex rooflines
Best Choice: Duragutter’s modular design, engineered for efficient installation and superior performance, makes it a top choice for architects and builders alike.
How Architects Can Elevate Their Gutter Specifications
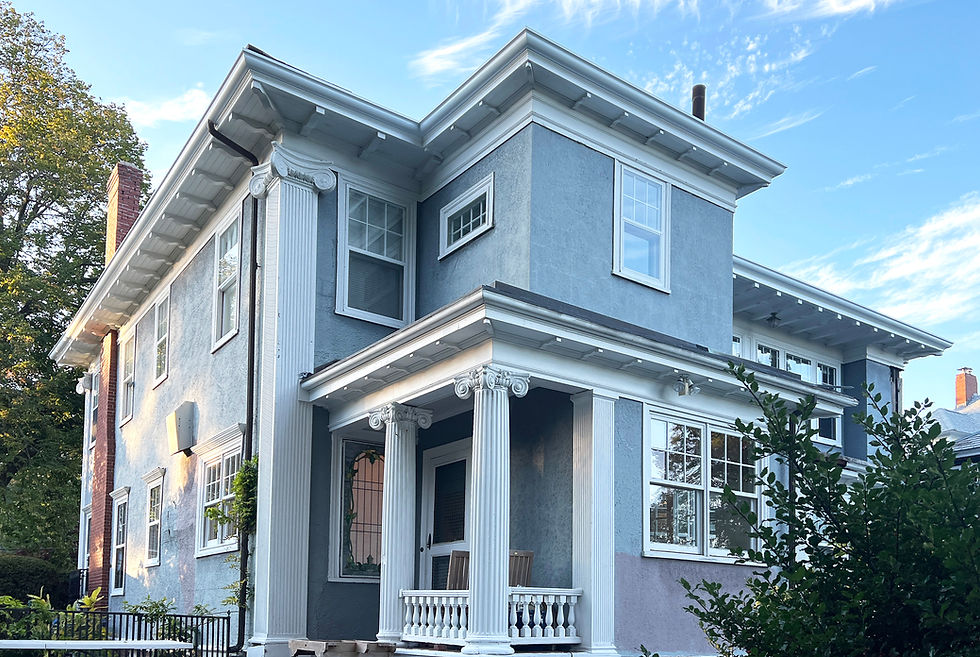
As an architect, specifying the right gutter system is just as critical as choosing roofing materials, exterior cladding, or window trim. With this in mind, here are a few ways to ensure the best results:
✔ Consider Gutters Early in the Design Process – Rather than an afterthought, gutters should be integrated into the design vision from the outset.
✔ Match Gutter Profiles to Trim Details – Select gutters that align with cornice moldings, fascia boards, or roof overhangs to maintain aesthetic cohesion.
✔ Specify Materials That Align with Longevity Goals – Choose materials like extruded aluminum, which offer decades of durability without the maintenance drawbacks of wood or copper.
✔ Ensure Proper Water Flow & Drainage Capacity – Work with engineers and builders to ensure optimal placement and functionality, particularly in climates with heavy rainfall or snow loads.
By considering these elements, architects can ensure that their luxury home designs are both visually flawless and functionally sound.
The Gold Standard for High-End Home Gutters
For architects seeking the best gutters for high-end homes, Duragutter stands as the premier choice. Trusted in historic districts across Massachusetts and approved for use on National Register properties, Duragutter combines:
Authentic architectural detailing
Premium extruded aluminum durability
Custom color matching for seamless integration
Easy installation for builders and contractors
Whether designing a historically inspired residence or a contemporary masterpiece, the right gutter system enhances architectural beauty, protects structural integrity, and adds lasting value to any luxury home.